No matter the industry or business, every manager or facility head looks for ways to improve their organization’s bottom line. For those part of the healthcare industry, additional cost savings can come in the form of the linen products being purchased and used. For example, disposable linen has become popular recently for its cheaper costs when compared to reusable linen. If your healthcare facility is trying to make ends meet, switching to disposable linen products is a reasonable idea.
However, what if your disposable linen products weren’t as “affordable” as initially advertised? In fact, what if all aspects of disposable linen vastly underperformed when compared to reusable linen? You’d be in for quite the shock! Well, here’s the truth: disposable linen products aren’t all they are hyped up to be. Allow Yamamoto North America to explain:
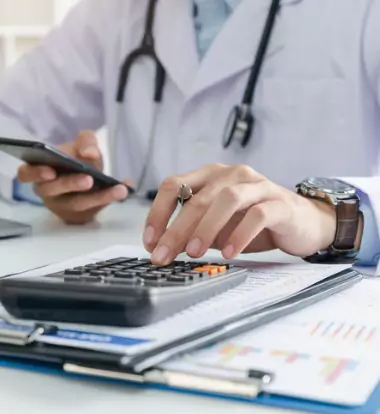
The True Costs of Reusable and Disposable Linen
When disposable linen first hit the market, its biggest draw was its affordability. Rather than spend thousands purchasing reusable linen and the machinery to launder it, you would only spend a fraction of the cost on the alternative without requiring extra equipment. If these cost savings continued well into your facility’s transition to disposable linen, it’d be hard to argue against its affordability. Yet, such isn’t the case.
While it’s true that reusable linen products have a higher initial cost, disposable linen is precisely as it says: disposable. This means you are stuck buying large quantities of new linen products each month as you toss out what has already been used. In turn, the repeated purchase of new linen continues to add up. Conversely, reusable linen is bought once and must only be replaced after numerous uses.
Also, while laundry equipment, such as that Yamamoto NA provides, is an added expense, the cost to launder your linen versus the cost to transport and dispose of linen is slightly lower. Surprisingly, this means it costs more for a facility to utilize disposable linen rather than rely on reusable products.
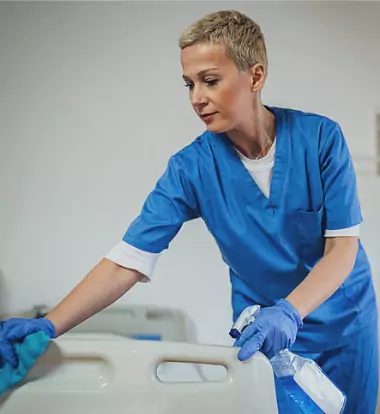
Do Disposables or Reusables Work Better?
Well, if you don’t save money using disposable linen, at least it’s more effective as a barrier between your patients and chemicals and waste, right? Unfortunately, this isn’t exactly true, either.
Disposable drapes and surgical gowns have the benefit of being microbe-barring, meaning they’re designed to keep infections and viruses out. However, where disposable textiles fail to perform is in their absorption ability. Because disposable cloth isn’t as absorbent as reusable, it can lead to greater messes during surgical or medical procedures.
While absorbability might not seem like an immediate issue, it matters for a health facility trying to uphold the highest sanitary standards. If liquids cannot be immediately cleaned, they risk the spread of infection and can cause unsafe working conditions for your doctors and staff. Reusable textiles, on the other hand, can more easily absorb liquids. Also, while single-use products may seem more effective on paper, properly laundered and sterilized reusable linens can provide just as much protection against microbes.
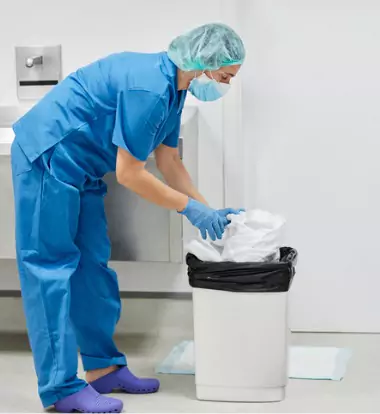
What About Environmental Impact?
Sadly, disposable linen isn’t getting much better in terms of its environmental impact. In fact, you can say that disposable cloth has the highest impact on the environment compared to reusable linen, which isn’t good.
First is how disposable linen is produced. Much of the materials and chemicals producing disposable, microbe-barring cloth are non-renewable resources. In other words, just manufacturing disposable cloth products drains our earth’s resources. This production process isn’t the most “carbon-friendly,” leading to an increased ecological footprint.
Second is the waste caused by disposable products. After the use of a gown or drape made from disposable cloth, where do you think those products go? That’s right, in the trash and, inevitably, our landfills. The unfortunate truth of disposable linen is that it does little more than offer a slight convenience to those using it while the resulting waste takes up space.
In turn, reusable linen isn’t tossed after one use. With the right laundry equipment (like Yamamoto’s industrial washers), a medical facility’s dirty linen can be laundered quickly and affordably. Modern laundry technology such as Yamamoto NA draws significantly less water and electricity, meaning any waste produced is minimal at best.
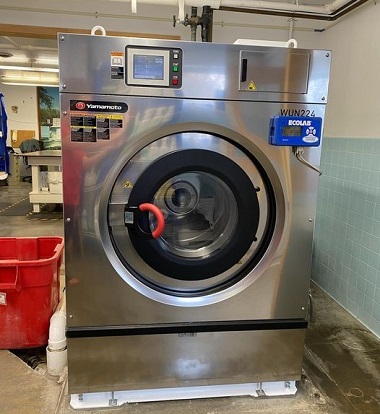
Secure the Right Equipment for Reusable Linen
Of course, if you plan to invest in reusable linen rather than waste time and money dealing with disposable products, you’ll require proper washing equipment. Fortunately, Yamamoto NA has precisely what healthcare facilities require! We manufacture high-quality industrial washers for affordable prices, helping our clients achieve peak cleanliness without breaking the bank. Best of all, our machinery emphasizes lower energy and water usage, helping laundry operators save on utility costs while protecting the environment.
Whether you wish to learn more about the differences between disposable and reusable linen, or you are interested in Yamamoto NA’s suite of washers, dryers, and automatic towel folders, you can call us today at
309-827-4303. Help your healthcare facility achieve greater cleanliness with reusable linen products and Yamamoto NA’s exceptional laundry equipment!